Tig welding—tungsten inert gas welding—can be defined in various ways depending on how one understands it. However, the traditional definition of tig welding is an electric manual welding procedure that uses a non-consumable tungsten electrode to create fusion energy between the metal and the wire filler material.
During the welding process, an inert gas is delivered by a gas nozzle to protect the weld pool, tungsten electrode, and the arc against harmful impacts by the ambient gases. Both direct current and alternating current are suitable for use with this kind of welding. Applications using tig technology span a variety of sectors, as discussed below.
Automotive sector
Automakers always put safety first while designing new vehicles. This guarantees that the cars remain functional and withstand the test of time. Tig welding has the benefit of creating rust-resistant metal fusion. The automotive industry extensively uses TIG welding services to prevent the rusting of essential vehicle components. Additionally, it makes the joints stronger, tougher, and safer.
When aesthetics matter, TIG enables the production of flawless welds thanks to its improved arc and weld puddle control. With TIG welding, one may precisely regulate the weld bead temperature by heating or cooling the weld puddle by depressing a foot pedal, much like when operating a car. Because of this, TIG welding is perfect for automobile parts production.
Aerospace industry
Both spacecraft and aircraft use magnesium metal as a component. Tig welding is frequently used in its manufacture due to its unrivaled strength and high precision. Tig welding can join the complex airplane components and the aircraft’s skin while preserving its highly prized aesthetic value. This is the most popular technique for welding aircraft parts.
Architecture and construction
Construction procedures today use more sophisticated and effective materials like steel and aluminum instead of traditional building bricks and concrete. The forerunner of this change was the skyscraper. These steel staircase railings and aluminum glass panels are created using Tig welding.
Art and craft
Art and craft are all about beautiful and appealing finishing. For sculptures and industrial repairs, a smooth finish is required to improve their aesthetic appeal. When creating artwork, tig welding is the preferred method. The majority of artists suggest it because it produces a solid structure with a smooth finish and works best with metals of thin thickness.
Food manufacturing industry
ISO 22000 mandates the use of stainless steel in all manufacturing and packaging procedures. Tig welding is the best method for creating and mending stainless steel-made machinery and packaging. A fundamental understanding of the food industry engineering is needed.
TIG welding does not produce smoke or fumes except when welding base metal that contains impurities or components like oil, grease, paint, lead, or zinc. According to welding experts from Micro Weld Inc, cleaning the base metal is necessary before welding.
Nuclear and power industries
TIG welds are excellent for essential seals because they are strong and resistant to corrosion and cracking.
Conclusion
TIG welding is more versatile compared to other techniques. Copper, bronze, brass, steel, aluminum, and bronze are just a few materials that work well with the method. This is partly because a welding professional has more control over the weld. After all, they can modify the heat used.
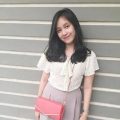
Laila Azzahra is a professional writer and blogger that loves to write about technology, business, entertainment, science, and health.