Flanges are used in place of welded connections to enable maintenance operations since they can be dismantled quickly and conveniently, unlike other mechanical connectors. As a result, they are commonly used in temporary or moving installations, dismantling piping systems, transitions between dissimilar materials, or connections in areas unfit for solvent cementing.
Since they are cost-effective, easy to understand, reliable, and available from various suppliers, they are the most common mechanical connectors. Similarly, their moment-carrying capacity is more significant than other connectors, making them suitable for systems that experience lateral buckling or pipe-walking due to pressure and temperature variations.
What are Pipe Flanges?
Basically, pipe flanges are bulging edges, collars, rims, or ribs used to join two pipes, a channel, and any fitting equipment. They come in different types and can be designed to meet various application requirements and functions, including corrosion resistance and high-temperatures. They are relatively simple and have proven to be effective in high-pressure piping applications.
Before shopping for the right flange, it’s essential to consider the amount of strength required for the flanged joint, as this will determine the correct piping flange dimensions and type.
Types of Pipe Flanges
Flanges mostly come in six different types. However, these designs can be modified to meet the specific functions and requirements of the applications. Therefore, it’s essential to understand the pressure at the flagged joint, the required strength, and the size of pipes involved. With the correct information comes six types of flanges that an individual can choose from. These include:
- Socket Welding (Socket weld)
- Threaded
- Lap on (Lap joint)
- Welding neck (Weld neck)
- Slip-on welding (Slip on)
- Threaded
Additionally, the flanges can be modified to form other types, depending on application and functions. These unique designs are made to incorporate specific needs and applications, like reducing flanges to answer to size and orifice flanges to incorporate orifice mounting. Other examples in this category include:
- Elboflange
- Weldoflange/ Nipoflange
- Swivel Flange
- Expander Flange
Let’s cover the major features of the main types of flanges.
1. Welding Neck Flange
They come with a long tapered hub that helps transfer pressure from the flange to the individual pipe and offer strength reinforcement to counter dishing. Their sturdy structure enhances their strength and stiffness, making them suitable for temperature and pressure fluctuation ranges, and they are ideal for high/low temperature and pressure pipelines.
2. Blind Flange
They are majorly used to seal the ends of pipes or valves. They have round faces and no central holes, making them suitable for blinding the pipelines. Similarly, they are designed to fit standard channels of various sizes and higher pressure rates than other types.
3. Threaded Flange
They are easier to attach to the pipe than other types. They’re threaded into the bore in line with the tube’s external threading and tapered to form a seal between the pipe and the flange. As a result, welding isn’t necessary for the process.
They are suitable for small pipes and low-pressure connections. However, they cannot stand very low or highly fluctuating temperatures. For effectivity, the flange needs to operate at a temperature not higher than 260° Celsius and not lower than ˗40° Celsius.
They are most common in galvanized street piping and were formerly used in the production of synthetic ammonia. They are not suitable for any system that could cause cyclic loading, crevice corrosion, or severe erosion. It’s also essential to avoid larger loads and high torques when using them.
4. Slip-on Flange
This design of flange slides over the end of the piping, after which it’s welded into place. They provide easy and cost-effective installation and suitable for low-pressure applications. Other applications include non-purifying compressed air and circulating water due to the ease of alignment.
5. Lap Joint Flange
Their main application is on pipes with lap joint stub ends. They never come into contact with the media and easily revolve around the tube, enabling easy alignment and assembly of bolt holes, even after completing the welds. As a result, they are ideal for systems that need frequent assembly of the pipe and flanges. Since they don’t touch the media, they’re more suitable for pipelines containing corrosive liquids and best for saving nonferrous metals, stainless steel, and other valued corrosive resistant material.
6. Socket Weld Flange
They are the best choice for high-pressure, small-sized piping. The fabrication of slip-on flanges is bigger than them, but their internal pocket permits better fluid flow and smooth bore. These flanges contain a fatigue strength 50% stronger than their double-welded slip-on counterparts when welded internally.
Alongside the six main types of flanges, we mentioned earlier that other special kinds are mostly modified to meet specific functions and applications. These include:
7. Weldoflange
A weldoflange is a combination of a weld neck flange and a weldolet. Unlike most flanges that special flanges that are joined by welding, a weldoflange is made by a single piece of solid forged steel
8. Nipoflange
A nipoflange is majorly used for branch pipelines. It’s manufactured from a combination of a weld neck flange and a forged Nipolet.
9. Swivel Flange
A swivel flange is available in all standard shapes, including lap joint, socket, weld neck, etc. Its main application is in enabling alignment of bolt holes between dual mating flanges, thereby assisting in the installation of pipelines with large diameters, including offshore and subsea pipelines, or pipework in shallow waters.
They’re ideal for gas, hydrocarbons, chemical, oil, water, and other challenging fluids in water management and petrochemical applications.
10. Latroflanges and Elboflanges
They are the most uncommon types of flange Olets. Elboflange is a combination of a letrolet and a flange, while a latroflange is a product of a latrolet and flange combination. They help in applications where a pipe needs to branch at 45 degrees.
11. Reducing Flange
Just as the name suggests, a reducing flange helps decrease a pipeline’s bore from one point to another or join pipes to other mechanical devices, including compressors, pumps, or valves with dissimilar inlet sizes.
The reducing flange can only decrease run pipe bore by two sizes. If that’s not enough for the application, then the ultimate alternative solution that involves a combination of a butt weld reducer and a standard flange may be considered. If a reducing flange can offer the desired results, then they are better in terms of cost.
12. Expanding Flange
They work in an alternating way as the reducing flanges. They are useful in expanding the bore of the pipeline from a given point to the other. Like the reducing flanges, an expanding flange also can only increase the bore by two sizes.
Categorizing pipe flanges
The most common way of classifying flanges is by considering their shapes. However, it’s essential to understand that there are other ways to categorize flanges, as these come in handy when durability, functionality, and application are in question. These include:
- Classification by material used includes brass, alloy steel, cast iron, carbon steel, stainless steel, aluminum, or PVC.
- Classification by flange face includes flat, ring joint, raised, female and male, lap joint, tongue, and groove.
- Classification by piping flange dimensions, which include pressure rating or nominal size.
- Classification by flange finish, which gives smooth, stock, or serrated.
How flanges operate
Flanges have flat or flush surfaces that are vertical to the pipe to which they are attached. The attachment process involves mechanically joining two or more faces using bolts, adhesives, collars, or welds.
Due to the attachment requirements, a flange must fit the equipment or pipe that it’s designed. That’s why it’s necessary to check all the possible specifications and dimensions to ascertain that it’s of the right size, type, and material.
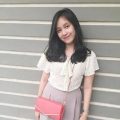
Laila Azzahra is a professional writer and blogger that loves to write about technology, business, entertainment, science, and health.