Micro laser welding is a specialty process that allows you to create small, precise details on your parts. With micro laser welding, you can control the power supply to have more accurate control over your work rather than just having it hit hard and fast like conventional industrial laser welding. Micro-laser welding has played a significant role in welding medical device components and other high-precision machined components. This article will discuss the advantages of the power supply control feature during laser welding.
1. Improve Micro Laser Welding Process Speed
The ability to control the power supply during micro laser welding is an essential advantage in the production process and dramatically impacts production speed. The faster the welding speed, the better quality of the welding product.
That is also a concern for manufacturers who want to produce high-quality products quickly. With the ability to control the power supply during laser welding, you can improve your production speed by optimizing your current equipment and using new technology to increase productivity.
2. Reduce Defects In the Welded Joints
In the past, it was common to see defects in welded joints due to power supply problems. The welds would be incomplete or have improper penetration depth because of the welding machine’s poor current quality. However, with the help of a micro laser welder, this problem has been solved.
The ability to control the power supply during laser welding can enable you to reduce defects in the welded joints and achieve a more precise result. That’s because when you control the power supply during laser welding, you can adjust it according to your needs, and thus, get better results.
3. Yields Higher Quality Micro Laser Welds
The ability to control the laser beam power supply helps reduce distortion and make the cuts cleaner. In addition to this, it also helps yield higher-quality micro laser welds. Power supply control during micro laser welding can help you produce high-quality micro laser welds with less distortion and less heat buildup inside your machine.
A professional laser and TIG welding company like Micro Weld, Inc will help you produce better looking cuts and ensure they are strong enough to withstand additional stress from subsequent layers of material you’re welding together. They will help improve overall quality in appearance, strength, and even longevity.
4. Better Control Over Your Processes and Parts
The ability to control the power supply is one of the essential advantages of the micro laser welding process. You can easily monitor the process and change it if required. You will have better control over the welds, which will help you create a high-quality part. You can ensure that the component gets a consistent amount of heat, which will ensure that it melts properly.
That will also help avoid excess heat or cooling of the components, which could lead to poor-quality welds. You will also be able to monitor the progress of your workpiece at all times. You won’t have to worry about your workpiece suffering damage or burning due to overheating. You can always ensure the process is orderly by tracking the power supply through the laser.
5. Ability To Reduce Heat Input
The ability to control the power supply during micro laser welding is a great advantage with a small price tag. With this feature, you can reduce heat input and improve the speed of your process. That means you’ll be able to produce better quality micro laser welds and yield higher results overall. You’ll also be able to control the heat sink better, ensuring that your parts will be airtight while being welded together.
Conclusion
The independent power supply control throughout the welding process makes it an attractive micro-laser welding method. Due to its versatility, this technique has found applications in many fields in engineering and medicine where laser performs better than existing technologies. The ability to control power with high precision also makes it possible to weld fine features in some instances. Larger scale applications include repairs in aviation turbines and sealing implanted medical devices.
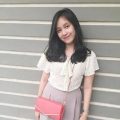
Laila Azzahra is a professional writer and blogger that loves to write about technology, business, entertainment, science, and health.