When is the last time the portable electric gadgets in your home, office, or work environment tested and tagged by a competent technician? Is this a necessary practice even when your appliances are sourced from a reliable manufacturer? This article will guide you through the details of electrical tagging.
What is Test and Tag?
Test and tag is the process of visually inspecting all portable electrical appliances to determine their suitability for individual use. It is a two-phase exercise. First, as the term suggests, you test the appliance by inspecting it for any damage, such as missing some essential parts. Once the item qualifies or fails the test, it is tagged to reflect its status.
Does one need to be an Electrician to Test and Tag?
Any employee who undergoes a test and tag training course is competent to carry out this exercise. The trainee needs to verse themselves with the up-to-date changes and development to equip themselves with new skills, from time to time.
How does it Work?
Long after purchase a high-quality appliance, a device can deteriorate and pose a danger to users. Test and tag process is done to:
- Check for discoloration due to heat, moisture, and chemical exposure.
- Look for flexible cords and pins and determine their flexibility
- Determine the integrity of insulation resistance
- Detect defects, damage, or modification done on electrical devices such as cord extension, sockets, plugs, accessories, and connectors.
- Detect any obstruction in ventilation inlets and exhausts
- Confirm that the current electricity rating in use and match with the plugs in place
- Check mains and leads for excessive charring and damage
- Confirm that operating control are aligned, secure, and appropriately identified
Is Test and Tag Necessary for new Appliances?
Test and tag is a mandatory operation in the following circumstances:
- Before using a brand new or second-hand appliance
- After receiving an appliance from repair works or regular servicing
How often Should test and tag be Carried out?
Generally, electrical tagging should be done every 3 months to 5 years depending on the functions of the appliance. For instance, tagging should be done every 3 months for construction and mining equipment. The inspection can be annual in other less intensive areas such as offices since devices are open to abuse or subject to regular use.
What Happens to an Appliance that Fails the Test?
After the routine testing, a faulty appliance is labeled and withdrawn from active use. The device can be forwarded for repair or disposed of for good.
Compliant equipment is safe for use. It should be fitted with a durable, non-reusable, and non-metallic tag with the following details:
- Name of the person who runs the test or
- The name of the firm which carried out the test
- Reference to the relevant testing standard
- Inspection date
- Re-inspection test for subsequent tests
The employer is always liable for employees’ injuries or accidents caused by faulty electrical devices. Therefore, test and tag is a necessary precautionary measure to protect both parties.
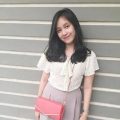
Laila Azzahra is a professional writer and blogger that loves to write about technology, business, entertainment, science, and health.