Behind the dance of logistics, with goods going from storage to transport with the ease of clockwork, three essential mechanisms quietly assist the operation. The elevator, the overhead doors, and the dock levelers often don’t take center stage, but without them, cargo movement would grind to a halt. In this guide, we walk you through how each one works, when each shine, and where each is limited, especially among the busiest environments of warehouses, storage facilities, and transportation terminals.
Why the Elevator is More than just a Lift
At warehouses that are more than a few storeys high—or city warehouses where space is most valuable and going vertical is the only choice—the elevator becomes an absolute design component. But it’s something greater than a box hung by cables. Logisticians’ elevators are engineered with bearing loads, repeat usage, and integration into larger inventories.
Advantages include-
- Efficiency- \Reduces movement time for forklifts and manual labor.
- Safety-Reduces the potential for danger by eliminating the need for ramps or stairs.
- Space-Saving- Utilises maximum vertical space, valuable in high-density or city locations.
- Smart Integration- Often programmable for semi-auto or auto schedules.
Disadvantages include
- Cost-High upfront and regular maintenance costs.
- Downtime Risk- A mechanical breakdown freezes upper-floor access.
- Installation Difficulty-Retrofits of current buildings are complex and costly. In short, when your facility grows upward, the elevator isn’t a nice-to-have, it’s a necessity. It just needs care, and it needs investment.
How Overhead Doors Shape Warehouse Flow
While goods move horizontally, from sortition areas to receiving bays or wait trucks, they pass through a critical junction point, the overhead doors. Often neglected, the doors regulate the pace, security, and even the energy efficiency of the operation.
Advantages
- Ceiling-Saving-Vertical motion saves drive-throughs and headspace.
- Insulation & Protection- Climate-controlled and weatherproof interiors.
- High Frequency Ready-Built to open and close during the day without stress.
- Automation-Choices for sensors, remotes, or even phone control.
Disadvantages
- Maintenance-intensive- Tracks, springs, and seals wear out over time.
- Alignment Issue-Will jam or misfire, temporarily halting operations.
- Environmental Impact-in cold or dusty environments, seal failure results in power losses or contamination.
For facilities with regular loading/unloading schedules, the right overhead door isn’t just security- it’s pace. An appropriately installed door keeps the operation’s pace and continuity intact. A forgotten one? It’s everyone’s worst choke point.
The Unsung Bridge-Dock Levelers
Typically, at the level of the warehouse floor and nearly invisible until in operation, dock levelers are modest pieces of equipment with a purely essential task. They connect your fixed facility floor with the ever-changing truck heights of incoming and outgoing trucks.
Advantages
- Flexibility- Accommodates various weights and heights of trailers.
- Security-Prevents gaping, slipping, and jerking during loading/unloading.
- Robustness-Designed to withstand heavy forklifts and everyday wear.
- Time Efficiency-Saves time and reduces worker fatigue.
Disadvantages
- Precision Required-Accidents may result due to poor installation or recalibration.
- Costly Maintenance Needs-Hydraulic or mechanical components deteriorate over time.
- Massive Consequences of Failure- A faulty leveler can stop a whole shipping schedule.
Even despite these considerations, the importance of dock levelers cannot be understated- they don’t only span trucks to warehouses, they bridge safety to speed.
Costing, Maintenance, and Repairs-What to Know Before You Commit
If new equipment is being installed or existing equipment is being updated, there are significant implications throughout the life-cycle—especially with costing, maintenance, and repairs. Up-front cost is based on size, technology, capacity, and automation level. Intelligent-diagnostics equipped elevators and MRL equipment tend to have greater up-front install cost but potentially reduced long-term servicing cost. High-speed or insulated overhead doors cost accordingly for greater thermal efficiency or increased speed. Dock levelers vary by unit type—mechanical types are lower cost up-front but are more hands-intensive with high-cost hydraulic types.
Maintenance ensures that your long-term investment does not go to waste and involves not just scheduled inspections, protective feature recalibration, and regular lubrication of parts as well. Elevators need certified tech visits to keep cables, control systems, and brakes intact. Overhead doors need track, spring, and sensor maintenance. Dock levelers need hydraulic check-ups and structural inspections before they lead to expensive loading interruptions. Repairs, when they happen, are deferred with preventive maintenance. Neglect accelerates wear and tear and abrupt, expensive failures, where high usage points are particularly susceptible to damage.
Facility managers who are proactive take these regular expenses and service intervals into consideration from day one. Everything starts with forward-thinking planning: investing money in quality equipment, budgeting maintenance that spans years, and securing agreements with certified service providers.
On initial inspection, the elevator, overhead doors, and the dock levelers look like inert infrastructure as mere building components on grand ports, premises and warehouses. In reality, however, they are key participants in the logistical dance of products movement. They bear the burden of high-speed operations, big volumes, and worldwide efficiency.
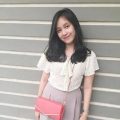
Laila Azzahra is a professional writer and blogger that loves to write about technology, business, entertainment, science, and health.